
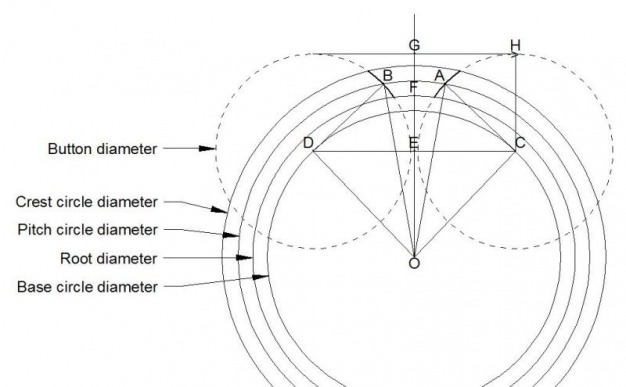
The mirror-finish area increased with the load, but the wear rate was almost equal to the result at low load. Tooth profiles as the result of high load contact. 4(c), some parts are still fairly smooth, but measurements show reduction in the over-all surface waviness especially in dedendum, increasing the Rz number of larger area.įig.
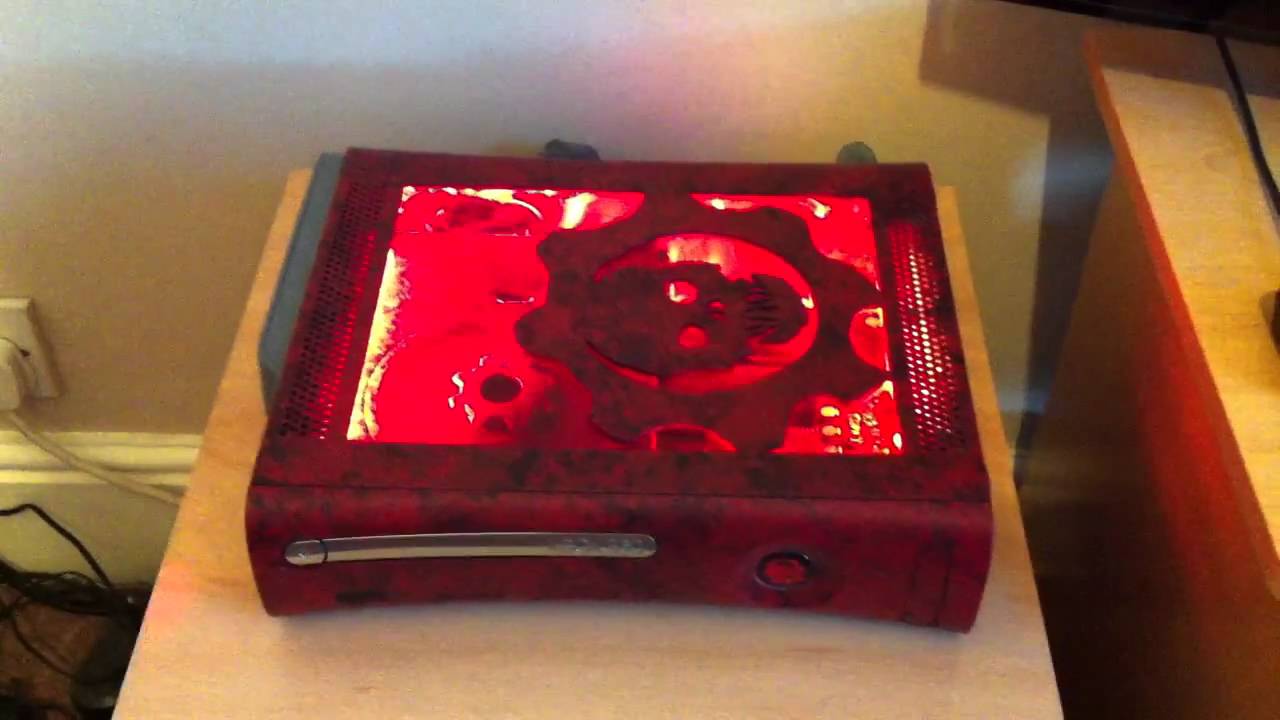
By further continuous wear, after 30000 revolution, however, specific areas of the surface were over worn below the calculated surface. 4(b) indicates that the suitably treated tooth surface is very smooth in local areas with the mesoscopical roughness matching the macroscopic involute curve well. Figure 4 presents 3-dimensional expression of the surfaces (a) before water-lubrication and (b) after 20000 evolutions showing close to the best-fit profile, while (c) reveals the over-worn surface after 50000 revolutions. Over tins range, the entire tooth surface was smooth but the profiles were much more worn than the calculated ideal involute curve, as is shown in Fig. A smooth profile closest to the ideal involute profile was obtained between 15000–20000 revolutions.
HOW TO MAKE INVOLUTE GEARS PLUS
3, the profile of (a) the original surface (shaved before treating) is indicated, plus me results of (b) worn surface after 20000 revolutions, and (c) after 50000 revolutions.
HOW TO MAKE INVOLUTE GEARS HOW TO
Now, it is a research subject of the author how to increase the number of contact teeth of the HGR through finding a suitable involute tooth profile. Maybe this is the main reason why the HGR cannot be used widely in industry like the TGR. Of course, torsional rigidity and overloading ability of the HGR are also lower than the TGR. This is because the number of contact teeth of the HGR is less than that of the TGR because of using the involute profile. The HGR has lower load-carrying capacity than the TGR. Transmission ratio of the HGR can be calculated in the same way as the TRG. This is because it is simpler to make the involute teeth than to make the trochoidal teeth.

The HGR can be made simpler than the TRG. When involute curves are used as tooth profiles of the external and internal gears, the TGR becomes the HGR. Only difference is the tooth profile curves. From Fig.3, it can be found that kinematics of the HGR is just the same as the TGR. Figure 3 is a structural example of the HGR. HGR is a planetary drive with small tooth number difference. The dead volume in the flapper valve is 21% of that in the reed valve. Moreover, we can reduce the dead volume which increases the recompression loss by minimising the volume of the release port. The pressure loss estimated form this simulation in the flapper valve is 27% of that in the reed valve. This is because a cross-sectional area of the flow pass is narrow and thus, flow is choked at the reed valve. The reed valve has a wider high velocity area than the flapper valve. A darker shade (red) indicates high velocity and a lighter shade (blue) shows low velocity. The brightness of the path lines expresses the flow velocity. Figure 7 shows the results of flow simulation using commercial software. By optimising the spring constant, we can reduce the pressure loss without any decrease in the reliability of the valve system. The spring constant can be changed easily by selecting the spring. The flapper valve consists of a valve, a spring and a stopper. Therefore, we developed a new valve system that is more effective than the reed valve system in reducing the over-compression loss.įigure 6 shows the new flapper valve system we applied. This pressure loss causes the over-compression loss. Because of the high spring constant, large pressure loss occurs when the reed valve is bent. The strength of the valve decreases when it is designed thinly to lower the spring constant. The reed valve has a simple structure but it cannot lower the spring constant due to the valve reliability. When the pressure in the compression chamber is higher than the discharge pressure, the valve releases the refrigerant from the compression chamber into the main chamber containing the discharge pressure.
HOW TO MAKE INVOLUTE GEARS FREE
The free end bends to release the refrigerant in the compression chamber. The valve is a metal sheet and one end is fixed to the fixed scroll. The reed valve consists of a valve and a retainer. Figure 5 shows the conventional reed valve system used to prevent over-compression. Therefore, the valves that prevent over-compression are located in the fixed scroll. When the pressure ratio is lower than the compression ratio of the scroll compressor, over-compression loss occurs. Generally, the scroll compressor has its own compression ratio determined by the length of an involute curve. The pressure ratio of discharge pressure and suction pressure is low at half-load conditions.
